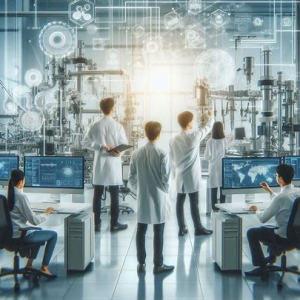
Optimizing API manufacturing is crucial for ensuring the consistent production of high-quality APIs. The pharmaceutical industry has learned valuable lessons from various strategies and technologies that have significantly improved the efficiency, precision, and sustainability of API manufacturing processes.
De-Risking API Strategy
De-risking involves minimizing the uncertainty and unknowns in an API strategy. This involves evaluating multiple options based on current data and knowledge, recording risks and assumptions, and selecting the best path forward. De-risking helps in enhancing timelines and success rates, adding value to the product and process.
Failure Mode Effects Analysis (FMEA)
FMEA is a powerful tool for identifying and prioritizing product risks. It involves breaking down complex processes into manageable steps, identifying undesirable effects, and quantifying the impacts of these failures. FMEA helps in reducing, controlling, or eliminating potential failures by understanding product and process parameters.
Scalability of Raw Materials
Scalability of raw materials is critical in API manufacturing. Companies should define how their API production will scale up throughout the drug discovery program. Not all raw materials are scalable, and some may have health, cost, or safety implications. Identifying scalable raw materials and using them in the chosen route simplifies the scale-up process.
Process Optimization
Process optimization is essential for ensuring the quality and efficiency of API manufacturing. This involves understanding critical parameters, optimizing processes, and performing proof-of-concept studies. Statistical design of experiments is particularly useful for identifying interdependent variables and ensuring consistent quality attributes.
Continuous Manufacturing
Continuous manufacturing is a cutting-edge strategy that allows for a more streamlined and efficient production process. This approach is driven by regulatory expectations and the need for cleaner, more flexible, and more efficient processes.
Quality by Design (QbD)
QbD emphasizes the systematic development of processes to ensure quality is built into the product from the beginning. This involves identifying critical process parameters and developing robust processes that minimize variability. QbD helps in achieving better control over API production and reducing the likelihood of deviations.
Automation and Data Integration
Automation and data integration play a vital role in optimizing API manufacturing. Automated systems enhance precision and speed by reducing human error, and the valuable data generated can lead to more efficient production through real-time monitoring and process improvement.
Collaboration and Knowledge Sharing
Collaboration between pharmaceutical companies, research institutions, and technology providers is crucial for leveraging collective expertise and developing innovative strategies. This includes sharing insights and innovations, adopting cutting-edge equipment and processes, and developing novel manufacturing techniques.
Sustainability
Sustainability is becoming increasingly important in API manufacturing. This involves reducing waste and energy consumption by developing greener technologies and materials. Pharmaceutical companies that can successfully navigate these challenges are likely to thrive in the evolving market.
Lessons Learned
The industry has learned valuable lessons from various strategies and technologies. For instance, Brian Chekal, an expert in API manufacturing, emphasizes the importance of understanding chemical processes and adopting advanced process technologies like continuous manufacturing and QbD. He also highlights the role of automation and data integration in optimizing API manufacturing.
Expert Insights
Industry experts like Goeddel from MilliporeSigma and Stolle and Poechlauer from Patheon emphasize the need to consider factors such as raw material supply chain, process safety, and projected future API manufacturing costs when deciding whether to use an existing synthetic route or develop a new one.
Conclusion
Optimizing API manufacturing is a dynamic journey that requires careful consideration of various factors. By adopting cutting-edge strategies like continuous manufacturing, QbD, automation, and data integration, pharmaceutical companies can ensure the consistent production of high-quality APIs while reducing costs and environmental impact.
Optimizing API manufacturing is a dynamic journey not a static goal. Pharmaceutical companies can navigate the evolving landscape of pharmaceuticals and continue to deliver innovative and life-saving drugs to the world by adopting these cutting-edge strategies. — Sollers Education.
References
- Optimizing your API strategy to deliver desired results. (2018, February 26). DrugPatentWatch.
- Optimizing API Manufacturing. (2016, August 31). PharmTech.
- API Manufacturing: Navigating Technological Advances and Regulatory Challenges. (2024, June 30). Sollers Education.
- Bringing API Manufacturing into Focus: Lessons Learned with Brian Chekal. (2017, February 23). The Medicine Maker.
- Optimizing API’s Manufacturing Process at Lab Scale and then to Commercial Production. Intellex.